Today I finished a small batch of carbide-faced file guides and I thought it would be funny to look at my past attempts to make a file guide.
In case you are not aware of this useful tool, you can check out this video: https://youtu.be/gh_Y74uQSwI?t=316
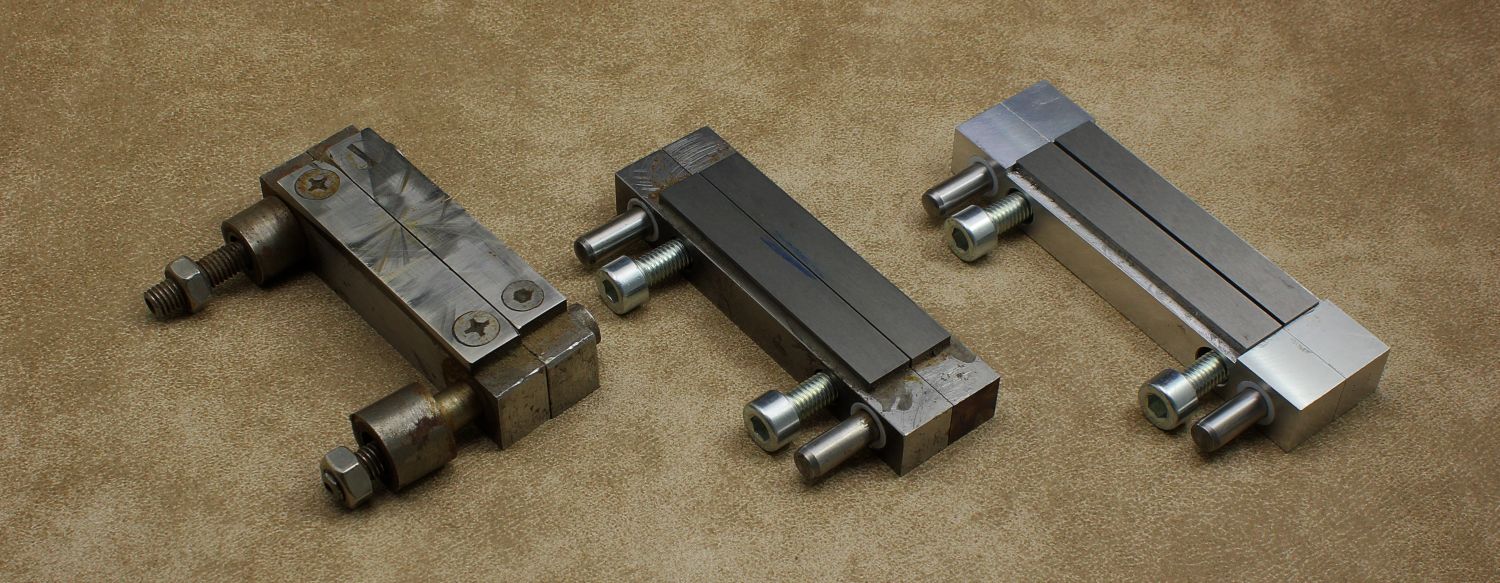
The first one I made (the left most one in the picture above) has to be more than 4 years old. It has D2 faces (63 HRC IIRC), masterfully attached using 3 (!) different types of screws. In my youthful arrogance I tried to make a guide pin that would also act as the tightening mechanism. I still think this should be doable and it would give the file guide a lot more capacity, however, back then my machining skills were simply not up to the task and in the second iteration (middle of the picture) I opted for the traditional pin (commercially available hardened dowel pin) and screw approach.
I believe I made the second iteration shortly after I purchased a milling machine, but I did not have a lot of luck using it. I struggled with getting the holes aligned correctly and getting them square. As a result the file guide does not run very smoothly. This time I went for carbide faces that I got from China – I bought a lot more than I needed as I thought I would be making more of these (at least I was right about something). They are merely glued onto the body – I experimented with hard soldering, but this just seems to work ok and is much less of a hassle.
On the right is the latest and greatest incarnation – aluminum body for easier manufacturing, teflon bushings adapted from the 2nd iteration, inset carbide faces. Not visible is a threaded hole in the bottom of each half of the main body, meant for attaching a holding support – say that you’d like to put a folder blade with only a short tang into the guide. Then you could increase the purchase on the whole fixture by threading a handle of sorts into the back of the file guide body.
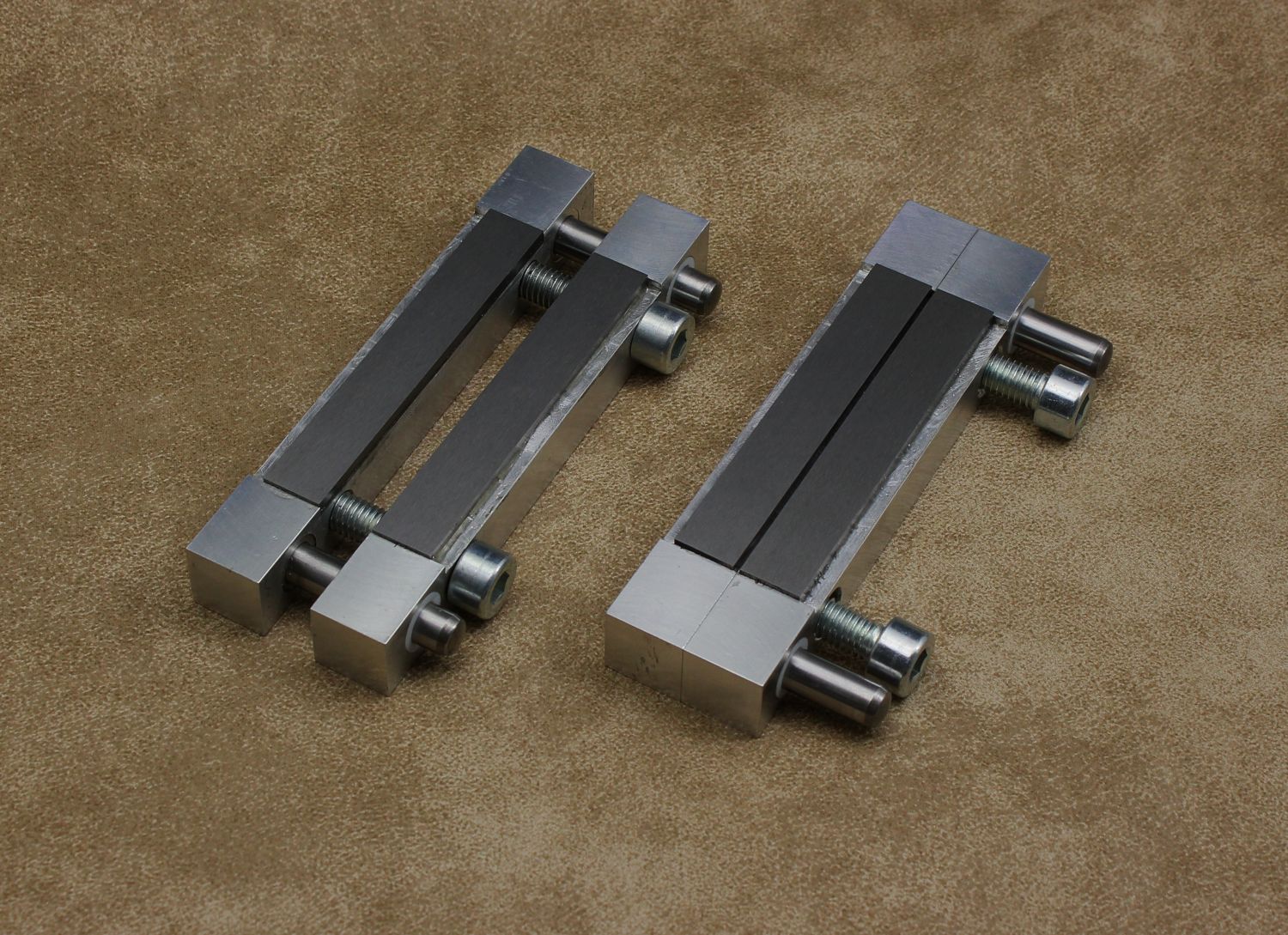
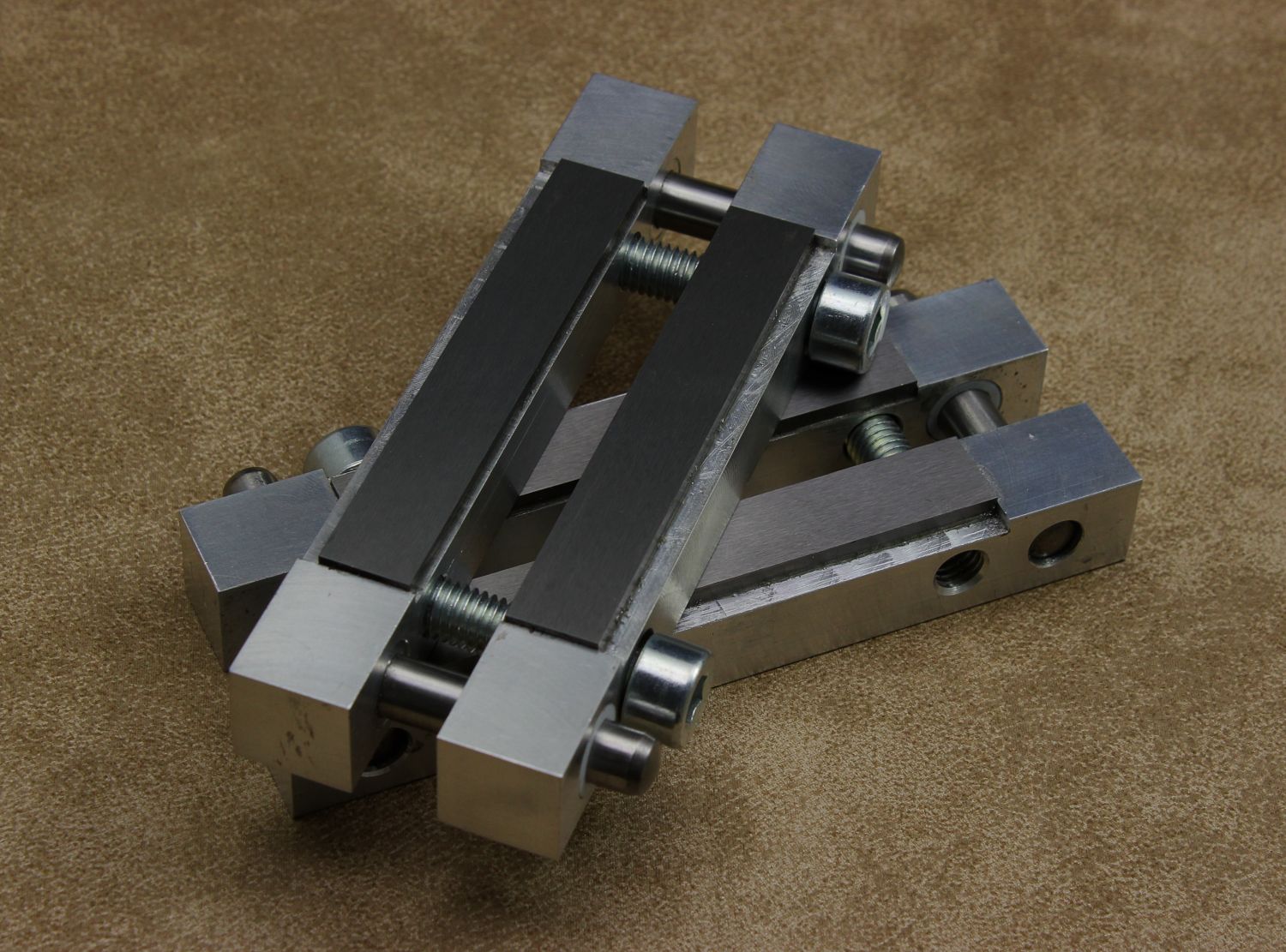
Cheers
-Pavel